
About Us
FAQ
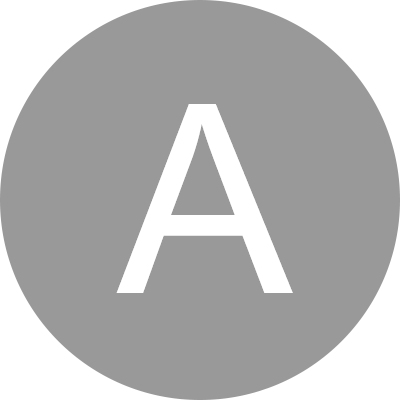
In the cosmetics industry, packaging quality is the second life of the product. Based on the characteristics of the cosmetics and sales conditions, suitable plastic tubes should be selected as the outer packaging for cosmetics.
1. Hygiene and Safety
Cosmetics come into direct contact with the human body, which imposes high hygiene and safety requirements on their packaging.
For plastic tubes, control should be exercised in terms of raw material safety, production processes, and production environments to ensure the hygiene and safety of the cosmetics contained within.
2. Protection
Packaging materials should have sufficient mechanical strength, a certain degree of barrier properties, chemical resistance, and weather resistance to prevent quality issues during the filling, storage, and transportation of cosmetics.
3. Economy
Among aluminum-plastic composite tubes, all-plastic composite tubes, and PE tubes, PE tubes are the cheapest compared to the other two types and can be adjusted for softness and hardness as needed.
Therefore, under the premise of ensuring good product performance, PE tubes should be chosen as much as possible to control the cost of cosmetics. Ailimei Plastic Products Co., Ltd. is a professional cosmetics tube enterprise integrating R&D, production, and sales, with a complete range of tube types, capable of producing PE double-layer tubes, PE five-layer tubes, aluminum-plastic sheet tubes, all-plastic sheet tubes, high-bright aluminum-plastic sheet tubes, high-bright aluminum-coated sheet tubes, and cosmetic accessories.
With advanced product molding, printing, and processing equipment, as well as a stable and efficient production team, we are committed to providing the market with stable quality and reasonably priced cosmetic packaging materials, allowing the company to maintain a leading position in the industry, with an annual output of over 100 million sets.
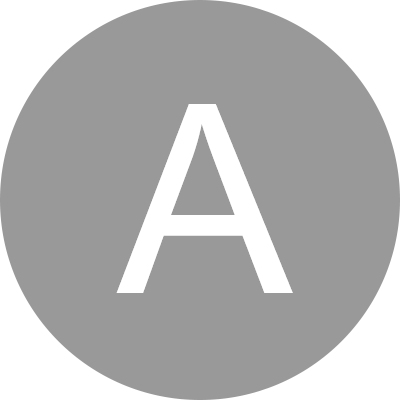
Elliptical tubes can be said to be closely related to people's lives, used almost every day, such as facial cleanser tubes, PVC packaging bags, cosmetic bags, clothing packaging bags, non-woven zipper bags, etc. But do you know how to correctly choose plastic packaging bags? Are you aware of some related common knowledge?
1. Hand cream tubes should not be mixed; corresponding plastic bags should be selected for different items. For example, food packaging bags are specifically produced for packaging food, and their raw materials and processes have higher environmental safety requirements. In contrast, plastic bags for chemicals, clothing, cosmetics, etc., have different manufacturing processes due to varying demands, and these types of plastic packaging bags should not be used for food packaging, as they can harm human health.
2. When purchasing plastic packaging bags, many people tend to choose thick and sturdy ones, but in reality, thicker is not always better. The country has strict standards for plastic packaging bags, especially those used for food packaging. It is essential to choose products produced by regular manufacturers and approved by relevant departments. Food plastic bags must be marked with "food-specific" or have a "QS mark." Additionally, you can check the cleanliness of the plastic by holding it up to the light. Qualified plastic bags are clean and free of impurities, while inferior plastic bags may show dirt and impurities.
3. Many people tend to choose aesthetically pleasing plastic packaging based on appearance and color, but this is also unscientific. Although there are many color varieties for plastic packaging bags, we must be cautious when selecting them. If the plastic packaging is for food items, it is essential to choose simpler colors, as this generally indicates fewer additives.
4. Regarding the reuse of plastic packaging bags. Many families have the habit of storing old plastic packaging bags. In fact, as long as you pay attention to neatness, storing and reusing old plastic bags is acceptable; it is both environmentally friendly and reduces waste. However, do not use old plastic bags for direct contact with ready-to-eat food, as this can cause chronic harm to our health.
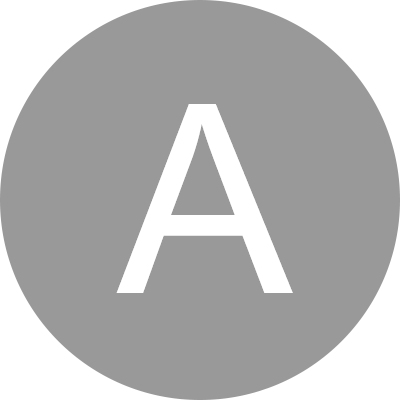
1. The characteristics of high-strength extrusion of the hose require the material to have excellent extrusion resistance; the hose material continuously pursues uniqueness and a good tactile feel. The deformation caused by sealing after filling requires the hose material to have even better flexibility to ensure a smooth and attractive appearance throughout the entire usage process.
2. The wide application fields of hoses, weather resistance, and attention to the contents; hoses need to withstand the harsh challenges of practical applications. For example, hoses used for sunscreen products must pass strict tests for sun resistance, high temperature, and high humidity.
In recent years, traditional metal and glass containers in the daily chemical industry have gradually been replaced by lightweight plastic hose packaging. The reasons for this can be found in the following advantages of plastic hoses:
Plastic hoses are hygienic and convenient to use, with bright and beautiful surface colors. Therefore, they have been widely used in the packaging of creamy cosmetics, such as facial cleansers, conditioners, hair dyes, toothpaste, and in the pharmaceutical industry for creams and ointments.
Plastic hose packaging is economical and convenient, easy to carry, even under high-intensity extrusion. Data shows that 60% to 70% of hoses are used in the cosmetics industry, 10% to 15% in the pharmaceutical industry, and about 5% in the food industry.
Therefore, how to better realize the product design concept through hose packaging, enhance the decorative effect of hose packaging, and quickly attract consumers' attention while fitting the brand's temperament has become an important topic for end users to consider.
Plastic hose packaging product structure
The main part of the plastic hose includes the shoulder, the tube (body), and the tail, while the tube part is often decorated through direct printing or cosmetic packaging hoses to carry text or graphic information, enhancing the value of the product packaging.
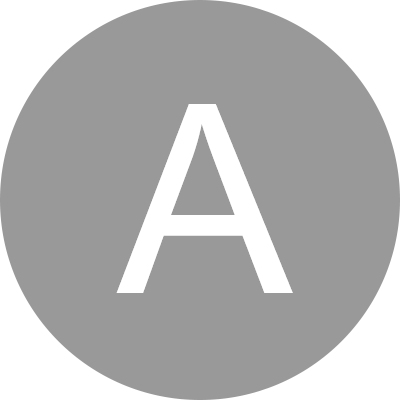
Currently, the commonly used plastic soft tubes in cosmetic packaging mainly include aluminum-plastic composite tubes, all-plastic composite tubes, and plastic co-extruded tubes. They can meet various needs of cosmetic packaging, such as hygiene and barrier properties.
1. Aluminum-Plastic Composite Tube
The aluminum-plastic composite tube is a packaging container made from aluminum foil and plastic film through a co-extrusion composite process into sheets, which are then processed into tubular form by a specialized tube-making machine. Its typical structure is PE/PE+EAA/AL/PE+EAA/PE. Aluminum-plastic composite tubes are mainly used for packaging cosmetics that require high hygiene and barrier properties, with the barrier layer typically being aluminum foil, and its barrier performance depends on the pinhole density of the aluminum foil. With continuous technological advancements, the thickness of the aluminum foil barrier layer in aluminum-plastic composite tubes has been reduced from the traditional 40μm to 12μm, and even 9μm, greatly saving resources.
The aluminum-plastic composite tube has the following advantages during use.
(1) High barrier properties. Aluminum foil has barrier properties such as light blocking, oxygen blocking, and water blocking, which can prevent external substances from entering the cosmetics, preventing oxidation and deterioration, while also preventing moisture or fragrance components from diffusing through the tube to the outside, thus ensuring the quality of the cosmetics.
(2) Low cost. To achieve the same barrier performance, aluminum-plastic composite tubes use less material than all-plastic composite tubes and plastic co-extruded tubes, resulting in lower costs and better economic efficiency.
2. All-Plastic Composite Tube
All-plastic composite tubes are made entirely of plastic and are divided into all-plastic non-barrier composite tubes and all-plastic barrier composite tubes. All-plastic non-barrier composite tubes are generally used for packaging low-end fast-moving consumer cosmetics; all-plastic barrier composite tubes usually have edge seams due to the tube-making process and are typically used for mid to low-end cosmetic packaging, with the barrier layer possibly being multi-layer composite materials containing EVOH, PVC, and oxide-coated PET. The typical structure of all-plastic barrier composite tubes is PE/PE/EVOH/PE/PE. The advantages of all-plastic composite tubes are as follows.
(1) Environmental friendliness. Compared to aluminum-plastic composite tubes, all-plastic composite tubes use economical and easily recyclable all-plastic sheets, which can reduce packaging waste pollution to the environment. Recycled all-plastic composite tubes can be processed again to produce relatively low-end products.
(2) Diverse colors. Depending on the characteristics of the cosmetics and different consumer demands, all-plastic composite tubes can be made in various colors, such as colorless transparent, colored transparent, and colored opaque, providing consumers with a strong visual enjoyment. In particular, transparent all-plastic composite tubes allow a clear view of the color state of the contents, creating a strong visual impact and greatly enhancing consumers' desire to purchase.
(3) Good rebound ability: Compared to aluminum-plastic composite tubes, all-plastic composite tubes have better rebound ability, ensuring that after squeezing out the cosmetics, the tube can quickly return to its original shape, always maintaining a beautiful and regular appearance. This is crucial for cosmetic packaging.
3. Plastic Co-Extruded Tube
Plastic co-extruded tubes utilize co-extrusion technology to combine different performance and types of materials into one shape. Plastic co-extruded tubes are divided into single-layer extruded tubes and multi-layer co-extruded tubes, with the former mainly used for fast-moving cosmetics (such as hand cream) that have high appearance requirements but low actual performance requirements, while the latter is mainly used for cosmetic packaging. The main advantages of plastic co-extruded tubes are as follows.
(1) Due to the absence of edge seams, the appearance effect is better than that of composite tubes, which is essential for cosmetic tube packaging.
(2) Depending on the shape of the extrusion die,
various shapes of extruded tubes can be produced, such as oval, square, etc., to meet different consumer needs.
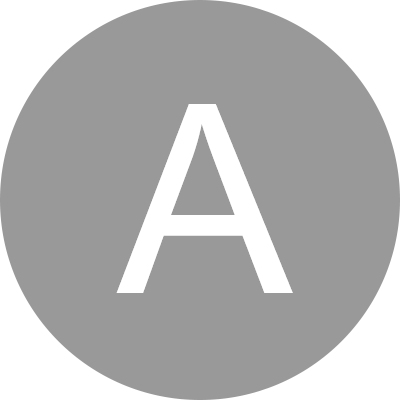
1. Glass
Glass bottles used for cosmetics are mainly divided into: skincare products (creams, lotions), perfumes, essential oils, and nail polishes, with smaller capacities; bottles larger than 200ml are rarely used for cosmetics. Glass bottles are further divided into wide-mouth bottles and narrow-mouth bottles. Solid creams are generally stored in wide-mouth bottles, which are suitable for aluminum foil caps or plastic caps, and the caps can be spray-painted for various effects; emulsions or aqueous creams are generally stored in narrow-mouth bottles, which are suitable for pump heads. If a cap is used, it should be paired with an inner plug; aqueous products should have small holes with the inner plug, while thicker emulsions should have larger hole inner plugs.
Combination forms:
1. Cream jar series: glass bottle body + double-layer plastic outer cap (generally with a capacity of 10g-50g)
2. Essence series: glass bottle body + plastic pump head or aluminum pump head (relatively higher capacity from 20 to 100ml)
3. Toner series: glass bottle body + plastic inner plug + outer cap (over 100ml, can also be equipped with a pump head)
4. Essential oil bottle series: glass bottle body + inner plug + large cap or dropper + dropper + aluminum cap
2. Tubes
Tubes are divided into single-layer, double-layer, and five-layer tubes, each differing in pressure resistance, permeability, and hand feel. For example, a five-layer tube consists of an outer layer, an inner layer, two adhesive layers, and a barrier layer. Features: it has excellent gas barrier performance, effectively preventing the infiltration of oxygen and odor gases, while also preventing the escape of the contents' fragrance and active ingredients.
Combination forms:
Tube + outer cap / tubes are commonly made of PE plastic. According to product thickness, they are divided into single-layer tubes (commonly used, lower cost) and double-layer tubes (better sealing performance). According to product shape, they are divided into round tubes (commonly used, lower cost) and flat tubes, also known as special-shaped tubes (require secondary joints, higher cost). Common outer caps for tubes include screw caps (divided into single-layer and double-layer, double-layer outer caps are often electroplated to enhance product quality and appearance, commonly used in professional lines) and flip caps.
3. Plastic bottles
The materials for plastic bottles are usually PP, PE, K material, AS, ABS, acrylic, PET, etc. They are typically used for cosmetic containers with thicker walls such as cream jars, bottle caps, stoppers, gaskets, pump heads, and dust covers, which are formed by injection molding; PET blow bottles are formed in two steps, while tube preforms are injection molded, and finished packaging is blow-molded. Other containers with thinner walls, such as lotion bottles and washing bottles, are blow-molded.
The above content is just a preliminary understanding; OEM manufacturers of cosmetics have professionals to explain it to you. Just remember the differences between the commonly used materials.
PET - PET has high transparency, the bottle body has some softness, can be squeezed but is harder than PP.
PP - PP bottles are softer than PET, easier to squeeze, and have lower transparency than PET, which is why some opaque shampoo bottles are commonly used (easy to squeeze).
PE - The bottle body is basically opaque and not as smooth as PET. Detailed explanation of OEM packaging materials is a must-learn course for cosmetics industry professionals!
Acrylic - thick and hard, the most glass-like material is acrylic.